Manufacture of pine splint basket from hand-split splints
Manufacture of pine splint basket from hand-split splints | ||||
---|---|---|---|---|
In the national inventory | ||||
|
Practitioners and people who know the tradition well
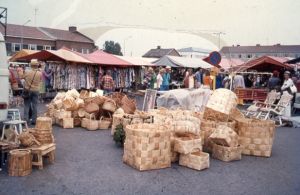
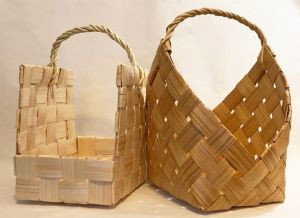
Traditional Finnish baskets are made from hand-split splints of Scots pine (Pinus sylvestris). These splints are woven together to create baskets of various shapes for everyday use, such as for carrying firewood, mushrooms, or groceries, and increasingly as interior decor items. The strength of these baskets relies on the interlocking of the splints, without the use of nails or rivets to attach the parts together.
The manufacture of splint wood baskets from felled pine trees to finished baskets is physically demanding work, which is why it has traditionally been done by men. The skill of basket making has been passed down from father to son, with fewer women engaged in this craft, often focusing on the weaving aspect. Today, baskets are increasingly being produced industrially using planed, cut and sliced veneer. Various types of carrying baskets are also woven from plastic "splints."
Splint wood baskets have primarily been made in rural areas because storing splint logs requires plenty of room, and the raw materials could be sourced from nearby forests. Until the 1940s, nearly every municipality in Finland had basket makers who produced them for sale or by order. In some regions of Finland, such as Veneskoski in Kankaanpää and Suur-Miehikkälä in Miehikkälä, basket making was a significant source of livelihood, and the skill was passed down through several generations. In the 1990s, Veneskoski had a professional community of around 30 people who made their living from basket making, and Suur-Miehikkälä had about ten.
The concentration of splint basket production in these areas can be partly attributed to the presence of state-owned old forests in the surrounding regions, from which logs could be purchased. In Miehikkälä, for example, it was still possible to buy splint logs from state forests in the 1990s, but in Kankaanpää, where basket makers were already numerous in the 1930s, timber for splints had to be purchased from neighbouring municipalities and later from Eastern Finland and Russian Karelia. Nowadays, old forests are protected, and it is difficult to obtain slow-growing, fine-grained pines suitable for splint wood baskets from commercial forests. The fast-growing pines in managed forests are not suitable raw material for splint baskets.
Prominent basket-making families in Veneskoski included Kallio, Lehtimäki, Ranta, and Talonen, while in Miehikkälä, multi-generational basket-making families included Korpela, Metsälä, Ramu, Rautamies, Takki, Toikka, Tuhkiainen, and Turu. Paavo Turu, a basket maker from Suur-Miehikkälä, was a renowned craftsman among basket makers and received the State Award for Art and Design in 1971. He also developed new basket models that were adopted by other basket makers. Miehikkälä basket makers even travelled to Kankaanpää to teach. The basket models have remained quite similar throughout different parts of Finland, but the name for the basket vary in different dialects: kori, keppu, kessi, koppa, vasu, and vakka.
Practising of the tradition
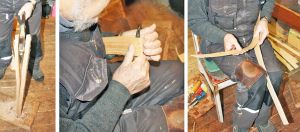
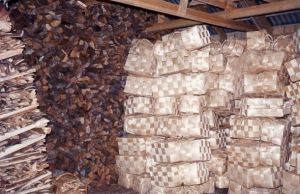
The tools needed for making splint baskets are basic hand tools: a saw for cutting wood and logs, an axe, smaller and bigger sledgehammers and wedges for splitting wood. In the process of splitting the splint, a sharp knife is used to create an initial groove from which the splints are hand-split. The knife is also used to shape the splints into even-width and thickness. Sandpaper and a mat or utility knife are used for finishing and trimming the baskets.
The most common basket models are made from flexible splints that are 5-8 centimetres wide, and they are woven by alternating the splints over and under each other in a plain weave pattern. Basket shaping can be done in two different ways: straight and diagonal weaving. In straight weaving, the splints fold at a right angle from the base, and separate weft splints are woven into the sides. In diagonal weaving, the sides are woven entirely from the ends of the base splints. Especially firewood baskets are made using diagonal weaving, where the side splints are at a 45-degree angle, and the rim is finished similarly to straight weaving. Diagonal weaving is common in chip and veneer baskets, where the edge is cut, and a separate rim splint is added by nailing.
The manufacturing of splint baskets is a multi-stage process. Preparatory work before splint splitting and basket weaving takes up about two-thirds of the total work time. The first and most crucial step is the selection of the three. Splints cannot be successfully split from pine that has grown too quickly or has an irregular shape. The best splint logs grow in sandy or swampy areas and have at least a 100-year-old trunk that is as straight and branch-free as possible, with dense, straight grain pine and the thickness of annual ring is no more than 1 mm. Slow growth, minor decay, and a small number of compression wood (lyly) or knots are not a problem. The tree is typically felled from October to March to ensure they remain fresh until spring. Tree felling in the summer can only be stored for about a month without becoming blue-stained and drying out too much. In this case, there is also a risk of fungal diseases and pests. In the summer, logs can be stored unpeeled in a mud pit or under water in anaerobic conditions, or they can be covered with sawdust or straw.
The length of the logs needed depends on the size of the basket; typically, a length of 0.8 to 1.5 meters is suitable for most basket models. The first 30-50 cm from the base of the tree is sawn off since the fibers are usually not parallel, and splint splitting would not be successful. After that, the fresh log is split radially into split billets, which are about 5-8 cm wide. Only the sapwood is used and the drier heartwood is removed from the billet, which
appears lighter in fresh wood. This results in a split billet ("pirkale," "rohno," "sorko," or "palho" depending the dialect), which is then split into shingles ("sale," "säle," "lohkare," "lompare") by splitting it in half along the direction of the growth rings. This process continues until splints about 1-2 mm thick are obtained. A knife is used to create an initial groove at the end of a splint, from which the splints are hand-split along the grain. The surface of the splint is smoothed with a knife, if it has ridges, and the edges are trimmed if necessary. Splitting starts from the top end, and as splints are split, resin rises to the surface to protect them from moisture and dirt, increasing the wood's durability. The finished splints can also be dried and used later for basket making if soaked the wood in warm water to make splints pliable and flexible before weaving.
The actual weaving of the basket is straightforward if the splints are of consistent quality and the wood is suitable. The wood should not dry out during basket making. Weaving begins with creating a square or rectangular base. When making the base, splints are always arranged with the heartwood side facing up, as this helps the splints to bend better. Splints are woven to the centre of the splint, alternately over and under each other, like a plain weave pattern.
A light slash is made with a knife on the outer splints of the base, and they are bent straight at a right angle against a sharp-edged wooden block. This creates the warp splints for the sides. The first splint in the side is cut at the corners in the same way as on the base's edges, resulting in sharp corners at the base of the basket. Depending on the basket's shape, subsequent layers can be woven either with sharp corners or rounded. The ends of the side splints are stacked 2-3 splint widths on top of each other and are thinned if necessary. This is done the same way if splints need to be extended. It is a good practice to make joint points on different sides for added durability.
For finishing the basket's edge, three splints are used side by side: First, the splint (“suuvanne”) is woven, similar to the previous warp splints. Its role is to stiffen the rim, and it may be narrower and thicker, with the heartwood side facing outward. The next two splints are woven on both sides of the first rim splint simultaneously. To finish the rim, the warp splints are turned over two of the splints and under the third alternately, both on the inside and outside of the rim. The end of the splint is carved with a knife for easier threading under the first, already turned warp splint.
The handle is made from two straight birch withes, each about 10 mm in diameter, and as evenly thick as possible, with a length of 1.5 meters. The bark is removed along the entire length so that the withe can be twisted without breaking. The handle is typically made from downy birch, which is more flexible and tough than silver birch. The handle is twisted clockwise starting from the top, and the remaining stubs and bark are carved off. The butt end is carved into a sharp point and threaded vertically into the top edge of the basket. The twisted withes’s tip is threaded through the opposite side's eye, and another similar withe is added. The withes are tightly twisted anticlockwise against each other. It's essential to pull the handle tightly, as it will loosen as it dries.
At the fold points of the base and the basket's opening, some wood fibers may break, and the vertical splinters are carved off with a sharp knife before being lightly sanded. The ends of the turned splints are cut by making a cut and folding them. After making the handle, the basket is allowed to dry outdoors in a cool place to prevent it from drying too
quickly. The basket is finished by sanding the fold points with fine sandpaper. During drying, the basket lightens by about 50%. The splints shrink primarily in width by about 6-8%, which increases the finished basket's eye size. The exterior dimensions of the basket remain nearly the same, with less than 1% shrinkage. For tight-weave baskets, the splints on the bottom need to be thin at the edges to weave them closely together.

The background and history of the tradition
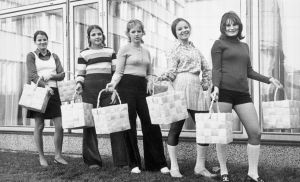
In Finland, splint wood baskets have been more common than willow and root baskets, and according to information obtained by the Manufacturing Board in 1857, the technique for making splint wood baskets was widely known throughout Finland. In rural areas during the 1800s, splint baskets of various sizes and shapes were used for different purposes. The most common were baskets used for carrying and storing items, but splint baskets were also used in fishing for various types of traps. The origin of splint baskets is not known, but in Sweden as well, splint baskets (known as "spånkorg" or "pärtkorg") have been common. The earliest records of professional basket making date back to 1489, although most basket makers were of German origin. The Swedish word "pärt" is derived from the Finnish word "päre," so it is reasonable to believe that splint baskets were made in Finland even earlier. In Sweden, baskets were typically diagonally woven, with the rim and handle attached with nails.
From the 1700s onwards, newspaper articles mentioned basket makers, called "koppa" and "vasu" masters, as well as various baskets as everyday items. Starting from the early 1800s, newspapers included instructions on using splint baskets for activities like sprouting potatoes, and there were even warnings about their unsuitability for storing hot ashes. At that time, pine shingles were commonly used as a source of light.
In rural areas, people made baskets themselves, but with urbanization, the growth of a market economy, and industrialization, the need for transport and storage containers increased, leading to professional splint wood basket manufacturing in different parts of Finland. Basket weaving was also an important source of additional income for small-scale farmers alongside agriculture and forestry. Both domestically made splint baskets and those imported from Russia and Sweden, often using Finnish wood, were sold in cities. Concerns about the sufficiency of wood and the preservation of forests existed already in the 1800s, and in 1845, the export of pine logs, spruce logs, and splint logs were prohibited.
Teaching splint basket making was often associated with providing employment for the unemployed and alleviating poverty. For example, in 1776, the Suomenkieliset Tieto-sanomat newspaper suggested that an executive arrange for men to engage in activities such as making splint baskets to earn a livelihood. In Central Finland, begging children were given splint logs so that "boys could try their skills in splitting splints and weaving baskets" (Keski-Suomi, 3.1.1885). There was also concern about unemployment in Helsinki, and the Helsinki Women's Association established Finland's first splint wood basket factory in 1892. Hand-split splints were purchased from rural areas, and about twenty basket weavers wove baskets ordered in advance, producing around three hundred per day for sale to merchants. Starting from the 1800s, basket making competitions were organized in connection with rural and home industry exhibitions.
In the early 1900s, there were several regions in Finland where specialization in basket making had developed. Making splint baskets was hard work; splints were split in the early morning, and baskets were woven in the afternoon. Companies bought large quantities at a time, and baskets were made to order for various purposes. For example, in the vicinity of Seinäjoki, hundreds of storage and transport baskets were woven for Itikka's meat processing plant, and in Kymenlaakso's Miehikkälä, bottle baskets were made for beverage factories and pharmacies. In the early decades of the 1900s, as many as 10,000 bottle baskets were made annually in Miehikkälä. Even during the war years in the 1940s, basket making was common, but gradually, due to a shortage of wood and the increasing use of plastic, the demand for splint baskets significantly declined. The price of splint wood had risen, and sourcing it from neighboring municipalities greatly reduced earnings. New utility baskets for household use were developed to replace previously made basket models, and laundry, firewood, and shopping baskets were common, and according to basket makers, they are still popular today.
The transmission of the tradition
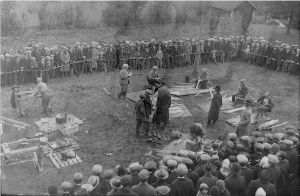
The production of splint baskets has declined, and commercial sales are now in the hands of only a few skilled artisans. The main challenge is the lack of closedense-grained splint wood. Occasionally, individual splint logs can be found from freshly cut-down pine trees, but spreading the tradition more widely is challenging. However, the weaving skill remains strong, as a wide range of materials can be used for it. Some splint baskets made from split splints are imported from Estonia and Russian Karelia, but the majority of baskets available for sale are made from industrially manufactured wood veneer or chips, with rattan used for handles.
In various traditional events, demonstrations of traditional splint basket making have decreased, leading to a decline in knowledge about the various stages of basket weaving. The skill that has been passed down from generation to generation is no longer being transmitted, and the preservation of the tradition is primarily dependent on individual basket makers and enthusiasts. In the 1990s, in addition to the basket makers in Miehikkälä and Kankaanpää, there were individual basket makers all over Finland who also conducted courses at community education centres. Nowadays, those who make baskets professionally are of retirement age, and the skill of basket making depends on a few individual enthusiasts. There is still demand for courses even today.
Safeguarding tradition
The viability of the tradition is faced with numerous threats and risk factors. The skill has typically been passed down from father to son, and baskets are made independently without a supporting community. There is little information available about the number of basket makers, whether they practice it as a profession, for additional income, or as a hobby.
In the 1970s, the municipality of Miehikkälä planned to provide splint basket-making education to help farmers find work during the winter months and earn extra income. However, professional basket makers were not enthusiastic about the idea, as teaching basket making was considered challenging, and there were concerns about their own livelihoods and declining prices. On the other hand, organizing courses was seen as difficult even then, as there was already a shortage of suitable wood for baskets.
Until the early 2000s, a few folk and community education centres organized splint basket-making courses lasting a couple of days. However, nowadays, only the Valkeakoski Institute in Luopioinen offers a two-day course twice a year. Since 2014, the instructor has been Raija Tiiva, from Kangasala, who began her own studies over ten years ago under the guidance of basket master Timo Nieminen from Pälkäne. In addition to splint baskets, Raija teaches willow basketry and spinning wool and linen on a spindle and/or wheel at the Valkeakoski Institute.
In the spring of 2023, there were eight participants in the splint wood basket course, some of whom had already attended Raija's previous courses. What the participants had in common were childhood memories of splint baskets in their homes and an interest in handicrafts. In the hands of a skilled maker, several baskets can be produced from a single log, but during training, the wood consumption for splitting splints is multiple times higher. "More kindling seems to be produced initially than splints suitable for making baskets," Raija says. The teacher's task is to provide pre-split logs. Preparations account for most of the work time related to splint basket production. Raija purchases the standing trees and personally cuts them down. She then drags the cut logs and branches to the roadside using a sled and processes the logs into splits for splint making before transporting them to the course location. However, before felling the trees, the quality and suitability of the wood for splint splitting cannot be assured. Organizing courses, including wood procurement and pre-processing, is labour-intensive, which is often not adequately reflected in teaching fees.
During summer heritage events across Finland, there are demonstrations of traditional handicraft skills, and occasionally, splint basket makers have showcased their skills. The Metsämuseo Lusto (Forest Museum Lusto) has also hosted demonstrations during the summer 2023. However, the craftsmen are reaching retirement age, and preserving their skills is of utmost importance. Although there are several photo collections of the different stages of splint basket making in museum collections, detailed documentation of crucial stages is lacking.
The skill of splint basket making is in the hands of very few skilled individuals. Professional production demands a lot from the maker, not only in terms of knowledge of wood but also sales and marketing skills. The current pricing does not allow for a reasonable livelihood. While people claim to appreciate authentic baskets made from hand-split splints, they are not willing to pay the price that would ensure even a reasonable hourly wage for the maker. Traditional baskets struggle to compete on price with veneer and plastic baskets on the market and splint baskets imported from Estonia.
How is tradition recorded?
Finland's museums have preserved a wealth of baskets traditionally made from hand-split splints. The technique and skill of splint wood basket making have been widely known throughout Finland. Even in the late 20th century, there was better availability of the material, i.e., slow-growing, dense-grained pine trees suitable for making splints. Baskets made from hand-split splints can be found in the collections of nearly every museum in the 2020s. The production of baskets for daily use and storage was common in both rural and urban areas until the 1950s. The baskets in museum collections were mainly made in the 20th century, primarily before the 1970s. In addition to everyday transport and storage
baskets, museum collections also contain items such as bottle baskets, weaving tool baskets, and even perch gutting baskets. Baskets made in the 2000s have been preserved in a few museum collections. For example, the Finnish Craft Museum has one splint basket made in 2010 by Simo Lappi from Northern Savonia.
In the collective finna.fi service of memory organizations, there are records related to splint baskets with the keyword "pärekorit": photos 785, objects 346, magazines/articles 46, books 37, videos 32, sheet music 17, sound recordings 10, artworks 10, archives 5, other undefined items 2, and theses 2. (https://www.finna.fi/Search/Results?lookfor=p%C3%A4rekorit&type=AllFields as of March 2, 2023)
Museum collection records may mix traditionally made splint baskets with chip baskets, which are industrially planed from splint wood. During cataloging, there may not always be an understanding of the differences in materials and manufacturing techniques.
Archives of museums contain individual photographs or photo series depicting the splint basket-making process. Many of these photos were taken during demonstrations or various events. There are numerous photos of splint baskets from different decades when they were used for storage and transportation. Photos can be found, for example, in the Miehikkälä Museum, the Kankaanpää Museum, and many other museum collections. One special category includes photographs from the SA picture collection showing splint baskets made as part of auxiliary work on the frontlines during the Continuation War. The photos depict soldiers as splint workers, the process, finished products, and the transportation of splint products for sale using horse-drawn wagons.
There has been relatively little filming or video recording of the splint basket-making process. Some amateur enthusiasts have created film and video material that can be found in local heritage archives and museum archives. For example, on Yle Areena, there is a short 4-minute video from 1969 showing the making of a splint basket by Paavo Turu. (https://areena.yle.fi/1-50197377) On YouTube, there are short videos showing various stages of the splint basket-making process, but the quality varies.
At least in the Kymenlaakso region, there is a DVD titled "Pärekoritaito" produced by the Kymenlaakso Arts and Crafts Association and filmed by Leo Märkälä in 1997. Another film, "Pölkyistä päreiksi," was created in 2007 by Seppo Rintela and Tero Viljasuo.
Interviews with skilled craftsmen related to splint basket making can be found in the archives of institutions such as the Kankaanpää Museum and the Folklore Archive of the University of Tampere. Designer Tiina Härkäsalmi has been conducting interviews with artisans who possess the skill of splint basket making since 2020. In addition to documenting the work process, she has also immersed herself in learning about the entire splint basket-making process, from choosing the right splint wood to the proper technique for splitting splints and making various types of splint baskets.
There is a clear need to document the knowledge and skills related to making splint baskets on video, starting from selecting suitable splint wood to the finished splint basket. The various stages of making splint baskets from split splints involve a lot of so-called tacit knowledge, which can be partially preserved for future generations through video recording. Research into the chemical processes that affect the long-term durability of splint baskets made from split splints is also necessary. Naturalness and sustainability are
important perspectives in the future of the handicraft industry. Preserving this tradition is the responsibility of the national responsibility museum, the Finnish Craft Museum, regional responsibility museums, and even small local museums. Splint basket makers should be supported and encouraged, and their expertise should be documented.
The future of the tradition
Few objects have retained their purpose for hundreds of years like splint wood baskets. A splint basket is a durable and lightweight carrying vessel that is easy to repair. It is completely non-toxic, and at the end of its life cycle, it can be safely disposed of by burning. It still serves a highly functional purpose as a firewood basket or an ideal mushroom basket since the mushrooms can remain airy in the basket. The basket is also easily repairable; by soaking it, you can disassemble it and replace the broken splints. The handle made of birch twigs is prone to wear and tear, especially in firewood baskets, but replacing it is easy.
The production of traditional splint baskets made by hand-splitting splints is disappearing. The old basket makers are already of retirement age, and the skill has not been passed on to the next generation. The problem also lies in the availability of pine trees with sufficiently dense grain suitable for splint making, which makes organizing courses difficult. Instead, baskets made from machine-cut veneer have become more common, but they are much weaker than those made from hand-split splints. However, the weaving skills have been preserved because veneer and chip baskets are woven in the same way as splint baskets.
Observing the work of these old masters reveals a tremendous amount of tacit knowledge that has been accumulated through decades of experience. Now is the last opportunity to document this endangered skill for future generations
The community/communities behind this submission
Five practitioners of the tradition
Bibliography and links to external sources of information
Bibliography:
Arponen, Outi. Opimme Punomaan: Tuohi-, Lastu- Ja Päretyöt. Espoo: Weilin + Göös, 1982.
Bühler, Waldemar (1962) Suuri askartelukirja II, Päretyöt s.14–25. Werner Söderström Osakeyhtiö , Porvoo.
Kautovaara, Pekka (2002). Kättentöitä. Kunnianosoitus kädentaidoille ja menneiden sukupolvien työlle. Otava, Helsinki.
Kautovaara, Pekka (1984) Käden taidot. Kunnallispaino Oy, Vantaa.
Lundgren, Anna-Greta (1987) Spånkorgar. Studiebok. Lts förlag, Tukholma.
Setälä, Vilho (toim.) Taitokirja. Kodin Taitosanakirjan uusittu laitos 1952, Otava.
Tuormaa, Markus (2014) Puutyöt – pärekorista pistoaitaan. Metsäkustannus Oy.
Virrankoski, Pentti (1994) Käsitöistä leivän lisää. Suomen ansiokotiteollisuus 1865–1944. Historiallisia tutkimuksia 186. Suomen historiallinen seura. Helsinki
Virrankoski, Pentti (1963) Myyntiä varten harjoitettu kotiteollisuus Suomessa autonomian ajan alkupuolella (1809– noin 1865). Historiallisia tutkimuksia LXIV. Suomen historiallinen seura. Väitöskirja. Helsinki
Articles:
Kanawa, 27.09.1845, nro 38, s. 1
Keski-Suomi 3.1.1885
Kotiteollisuus 1944 nro 4, s.-19-21 Pärekorit
Kotiteollisuus 1943, nro 1. Kauhat ja pärekorit
Suomenkieliset Tieto-Sanomat, 01.04.1776, nro 7, s. 4
Suomen Kuvalehti 12.8.1922
Suometar 3.2.1852
Uusi Suometar 26.3.1873
Videos:
Paavo Turu Miehikkälä ”Katoavia ammatteja”